Mechanical Vapor Recompression (MVR) Evaporators vs. Traditional Evaporators: A Comparison
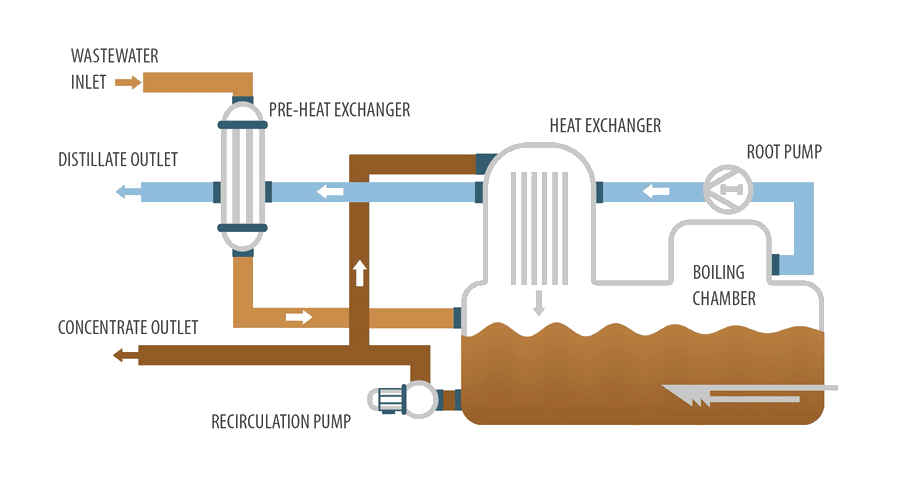
Evaporation processes play a crucial role in many industries, including food processing, chemical production, and wastewater treatment. The choice between Mechanical Vapor Recompression (MVR) evaporators and traditional evaporators can have significant implications for energy efficiency, operational costs, and environmental impact. In this comparison, we’ll explore the key differences between mechanical vapor recompression MVR evaporators and traditional evaporators, highlighting their advantages and limitations to help you make an informed decision for your industrial needs.
What Are Traditional Evaporators?
Traditional evaporators, such as single-effect and multi-effect evaporators, rely on external heat sources like steam to drive the evaporation process. In single-effect evaporators, the process uses heat once, while multi-effect evaporators use the vapor generated in one stage to heat the next, improving efficiency but still requiring a large amount of external energy.
Types of Traditional Evaporators:
- Single-Effect Evaporators: Utilize a single stage of evaporation, where heat is applied to evaporate the solvent or water from the solution.
- Multi-Effect Evaporators (MEE): Involve multiple stages (or “effects”), where vapor generated in one effect is used as a heat source for the subsequent effect, thereby reducing overall energy consumption compared to single-effect evaporators.
What Are Mechanical Vapor Recompression (MVR) Evaporators?
MVR evaporators represent a more modern and energy-efficient approach to evaporation. Instead of discarding the vapor produced during evaporation, MVR technology recycles and compresses it, turning it into a reusable heat source. This drastically reduces the need for external heat input, leading to significant energy savings.
Key Components of MVR Evaporators:
- Mechanical Compressor: The heart of the MVR system, it compresses the vapor to raise its temperature and pressure.
- Heat Exchanger: The compressed vapor is fed into a heat exchanger, where it heats the incoming feed liquid for continuous evaporation.
- Condensation System: After transferring heat, the vapor condenses, allowing the process to recycle water or other solvents.
Key Comparison: MVR Evaporators vs. Traditional Evaporators
1. Energy Efficiency
MVR Evaporators:
MVR evaporators are renowned for their superior energy efficiency. By compressing and reusing the vapor produced during evaporation, MVR systems can reduce energy consumption by up to 90% compared to traditional systems. This is particularly important in industries where evaporation is a continuous, energy-intensive process.
Traditional Evaporators:
Single-effect evaporators are the least energy-efficient, as they use a large amount of external energy (usually steam) and do not recover much heat. Multi-effect evaporators improve on this by recycling heat between stages, but they still require significant steam generation and fuel consumption.
2. Operating Costs
MVR Evaporators:
The higher energy efficiency of MVR systems leads to significantly lower operating costs. Since the system recycles vapor, the need for external energy sources like steam or electricity is minimized. This results in reduced fuel consumption, lower utility bills, and smaller carbon footprints.
Traditional Evaporators:
Traditional evaporators, particularly single-effect models, tend to have higher operating costs due to their heavy reliance on external heat sources. Multi-effect evaporators are more cost-effective than single-effect systems but still consume more energy than MVR evaporators, leading to higher operational expenses over time.
3. Capital Investment
MVR Evaporators:
The initial cost of installing an MVR evaporator can be higher than that of traditional evaporators due to the inclusion of advanced components such as the mechanical compressor. However, the long-term energy savings and reduced operating costs often offset the higher capital investment.
Traditional Evaporators:
Traditional evaporators generally have lower upfront costs, especially single-effect units. However, the long-term energy and fuel costs are significantly higher, particularly for energy-intensive applications. Multi-effect evaporators come at a higher price than single-effect systems but still require considerable energy input.
4. Environmental Impact
MVR Evaporators:
MVR evaporators offer substantial environmental benefits due to their energy-saving design. Lower energy consumption means fewer greenhouse gas emissions, which can help industries meet sustainability goals and comply with environmental regulations. Additionally, MVR systems often allow for water recovery, reducing water consumption and waste.
Traditional Evaporators:
Traditional evaporators, especially single-effect systems, have a higher environmental impact because they rely on steam generated from fossil fuels. The larger carbon footprint and water usage of traditional systems make them less environmentally friendly, although multi-effect systems are somewhat more sustainable than single-effect units.
5. Maintenance and Reliability
MVR Evaporators:
While MVR systems are more energy-efficient, they require a mechanical compressor, which adds complexity and maintenance requirements. However, modern compressors are designed to be durable and reliable, and the overall lower energy input reduces wear and tear on the system.
Traditional Evaporators:
Traditional evaporators are typically simpler in design, particularly single-effect systems. This simplicity can lead to lower maintenance costs and fewer mechanical issues, but the high energy demands may accelerate equipment degradation over time, especially in multi-effect systems.
6. Application Versatility
MVR Evaporators:
MVR technology is versatile and can be used across various industries, including food and beverage, chemicals, pharmaceuticals, and wastewater treatment. The ability to reduce energy consumption makes MVR systems particularly valuable in industries with stringent environmental regulations or high energy costs.
Traditional Evaporators:
Traditional evaporators also find widespread use in similar industries. However, for processes that require large-scale, continuous evaporation, their energy consumption may become a limiting factor. In smaller or less energy-intensive operations, traditional systems may still be practical, especially when capital cost is a primary concern.
Which Technology Is Right for You?
The choice between an MVR evaporator and a traditional evaporator depends on several factors, including the size of your operation, your energy consumption goals, and your budget for capital investment. If energy efficiency and long-term cost savings are your priorities, MVR technology is the clear choice. On the other hand, traditional evaporators may be more suitable for smaller-scale operations or industries where upfront costs are a key concern.
When to Choose MVR Evaporators:
- Energy-intensive processes: If your operation involves continuous evaporation and significant energy consumption, MVR evaporators can offer substantial savings.
- Long-term operational savings: MVR systems are ideal for industries looking to reduce utility costs over time, even if the initial investment is higher.
- Environmental sustainability: If your company is focused on reducing its carbon footprint, MVR evaporators are a greener choice due to their lower energy consumption and emissions.
When to Choose Traditional Evaporators:
- Lower initial budget: If your operation cannot accommodate the higher upfront costs of MVR systems, traditional evaporators may be a more budget-friendly option.
- Simplicity in design: For smaller-scale operations with fewer energy demands, traditional evaporators may provide sufficient performance without the need for complex vapor recompression systems.
Conclusion
Mechanical Vapor Recompression (MVR) evaporators represent a major advancement in energy efficiency, making them the preferred choice for industries looking to reduce energy consumption, lower operational costs, and meet environmental targets. While traditional evaporators may still be practical in some applications, particularly those with lower energy demands, MVR technology offers significant long-term advantages in terms of sustainability and cost savings.